How does that tie in to the triangular piece our group built in cartagena

If you compare the two photos you see that the triangular piece is is basicly a study how small can i make the P.K.Mehta concrete engineering and it will still work.
So it is not really about doing something “fundamentally different and unpoven” it is about changing the scale … but doing proven stuff…
As always the devil is in the details… questions arise
It is obvious how i do work a 30 cm concrete wall ( standard cast method ) but how do i make a wall that is only 4 millimeter thick ? - certainly the standard method of forming and pour in does not work here anymore…
If i have the rebar stick out in the big piece to connect the tension forces what size of fiber component connecting the tension forces do i work in the small piece ?
If the big piece can accomodate the “concrete code” rebar components need a 5 cm concrete cover to be protected against corrosion and avoid spalling
How do i handle the question of fiber component attack and spalling in a 4 mm wall it is obvious that i can not have 5 cm of cement cover over the fiber component of the composite.
What is clear from the picture is that the weight per cubic meter build is less in the triangular honeycomb piece than in the " foam cast" …
It is also clear that the triangle is “closed cell” that will not suck up water - while the foam is not.
Finally it is not written in stone that a honeycomb structure needs to be a slab on the watersurface you can also build something like this:
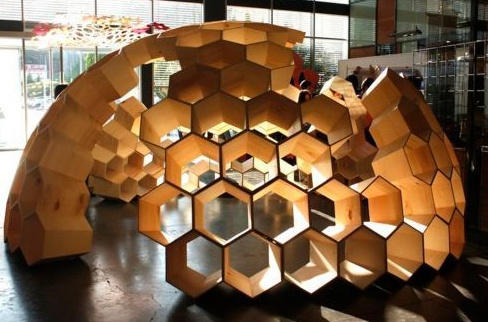
And from this it is a not so big a step to build this …
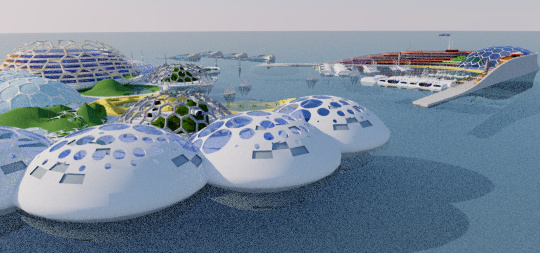
So when i say the floating city is unsinkable and acting like a foamblock… it is not that i recommend to actually build big portions of the city from some kind of messy foam material.
It is rather that everything is a “honeycomb structure of some kind” with closed cells and each cell floats.
They don’t let water seep from one cell to another - just like the pebbles in the styrofoam block float on their own, and no matter how you break it and how many cells you popp - it will never sink.
This kind of unsinkability - that does not depend on watertight sections and doors closing allows
to postulate a floating city that needs no rescue boats …
The building of ships is honeycomb structure building.
Even a 200 m ship is ok with a wall thickness of the cells of only 8-14 mm
So when you compare that to the triangle piece the similiarity becomes obvious… compared to steel concrete is about 3 times lighter, many times cheaper, and several times less prone to seawater damage.
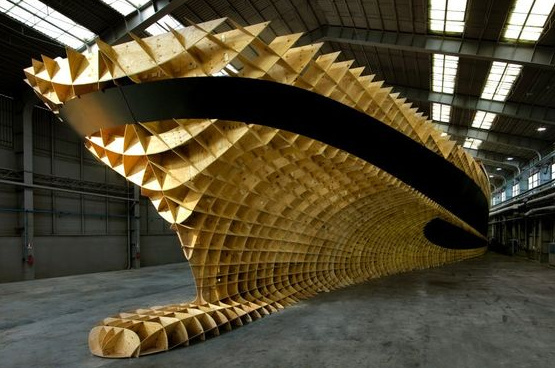
The honeycomb structure of the WHY yacht a project of Wally Hermes that is half way between floating island and yacht…
context | current engineering baseline for floating construction | condamine port extension | the normal land base concrete engineering applied on large scale for floating structures | straight forward applyable - no monsters lurking in the dark…
no weired dynamic effects created by waves - that normal concrete construction can not handle.